When you deal with the etching process, one big challenge comes from regions with different metal densities. Let me give you an example. In older processes, aluminum was commonly used for all interconnects. During etching, if there’s a low-density aluminum region next to a high-density one, the etch rate becomes uneven. The low-density region clears out faster, while the high-density area takes longer to etch. To make sure everything is etched properly, you might overetch, but this can remove too much material in the low-density areas.
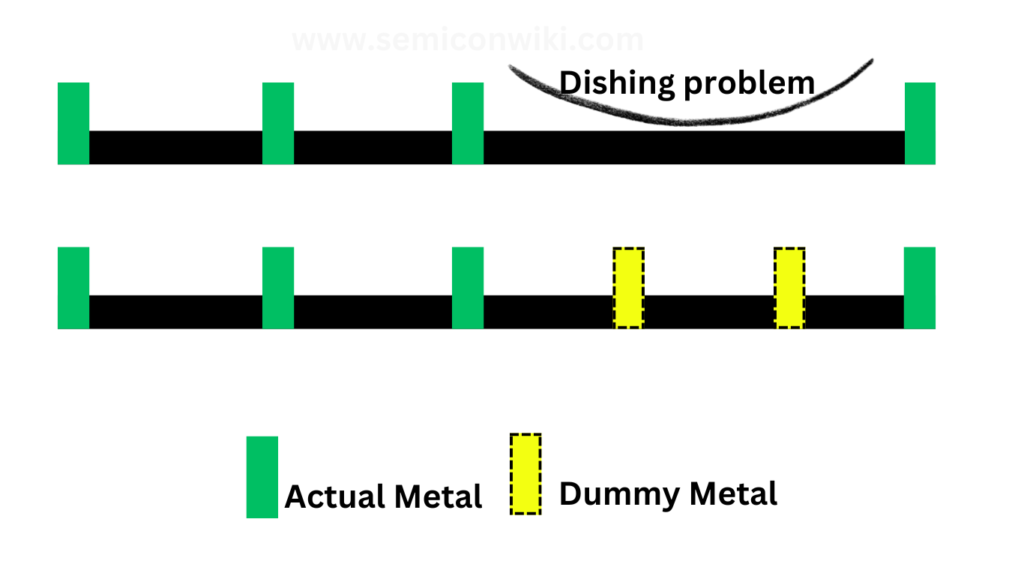
When you’re working on a layout, lower-density areas can cause “dishing” during the CMP (Chemical Mechanical Planarization) process. Dishing happens when too much material, like metal, is removed from less dense areas, making the surface uneven. This occurs because softer or exposed regions get polished more aggressively than dense areas.
What is Parasitic Channel Formation in MOSFETs: Causes and Solutions
How Dishing Affects Your Layout:
- Uneven Surface: Lower-density areas get over-polished, leaving recessed spots or “dishes.” This can mess up signal integrity and cause resistance to vary.
- Parasitic Effects: Uneven surfaces introduce parasitic capacitance and resistance, which can hurt circuit performance, especially in analog or high-frequency designs.
- Reliability Issues: Dished areas weaken interconnects, making them more prone to electromigration and failure.
- Manufacturing Challenges: Uneven surfaces complicate lithography and deposition steps, increasing the chance of defects in upper layers.
By handling lower-density areas wisely, you can minimize dishing and ensure a smoother, more reliable layout.
Dummy Fill in Layout Design
To fix this, we add dummy metals to balance the density across the wafer. These dummy metals can be inserted manually or automatically using a dummy fill script. This approach helps control the density gradients and ensures the etching process works evenly.
Morden Process
For modern copper (Cu) interconnects, the process is a bit different because we use a dual damascene method instead of the subtractive aluminum process. Here, the concern is more about the softness of copper. If the copper density is too high, the planarization step can remove excess material, leading to uneven surfaces. But just like with aluminum, adding dummy metals helps balance the density and prevent issues during fabrication.
In short, dummy metals are our solution for creating uniform density, whether we’re working with aluminum or copper interconnects.